World—Chip shortages create persistent challenge for manufacturers
A confluence of problems have led to persistent global semiconductor shortages, creating challenges for manufacturers. Before the COVID-19 pandemic, low capacity at existing foundries constrained semiconductor supply. Then, as the pandemic hit in early 2020, automakers reduced chip orders as vehicle sales plummeted. When demand recovered faster than anticipated in the second half of 2020, the semiconductor industry had already shifted production to other applications, including electronics products, to meet surging demand for computers and mobile devices (Chart). Other factors, such as storms damaging facilities in Texas, fires in Japan and drought in Taiwan (semiconductor manufacturing is water-intensive), have also hindered supply. Russia’s invasion of Ukraine compounds the problem. Russia produces 44% of global palladium supply and Ukraine produces 70% of global neon supply that are key raw material inputs into semiconductors. China’s COVID-19 lockdowns are also likely to contribute to further supply disruptions.
The current chip shortage is unlikely to be resolved quickly. This is because the production process is complex (involving a large network of firms) and developing new facilities is costly (for example, about US$20 billion for two new facilities in Ohio) and takes time (at least three years to become operational). For these reasons, the industry remains highly concentrated; Taiwan and South Korea account for over 70% of global semiconductor supply.
The disruption to semiconductor supplies may continue to impact products used in critical sectors such as health, defence and telecommunications. In response to this disruption, chipmakers are expanding production to meet growing demand, particularly in South Korea and Taiwan.
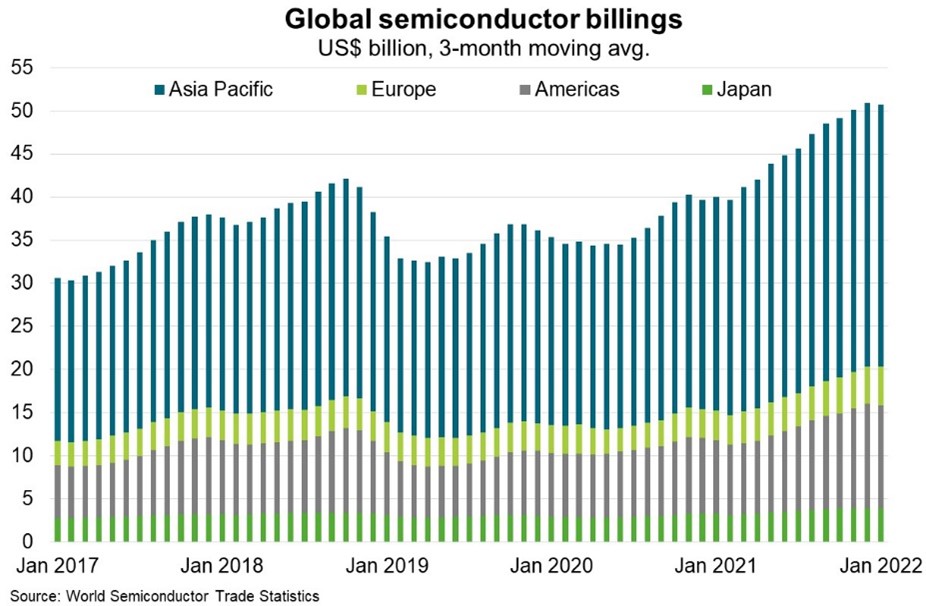